Porcea Stone’s team of experts has more than 20 years of combined experience in the landscaping industry. We specialize in premium outdoor porcelain pavers for residential and commercial applications. As a leader in product innovation, our main focus is on outdoor hardscaping products.
Our wide range of porcelain landscaping stones are designed for application in North America. They are made from the finest materials and engineered to last forever. Aside from this, we take pride in offering our clients exceptional customer service and custom-made solutions to suit their style and budget.
We are consistent with our ground-breaking designs and high technical standards of our products, along with our inherent emphasis on continuous innovation. Because of this, Porcea Stone has become synonymous with excellence in the industry.
A lot has changed over the years we have been in business. Nevertheless, our passion for providing you with premium products and outstanding customer service remains at the very core of what we do.
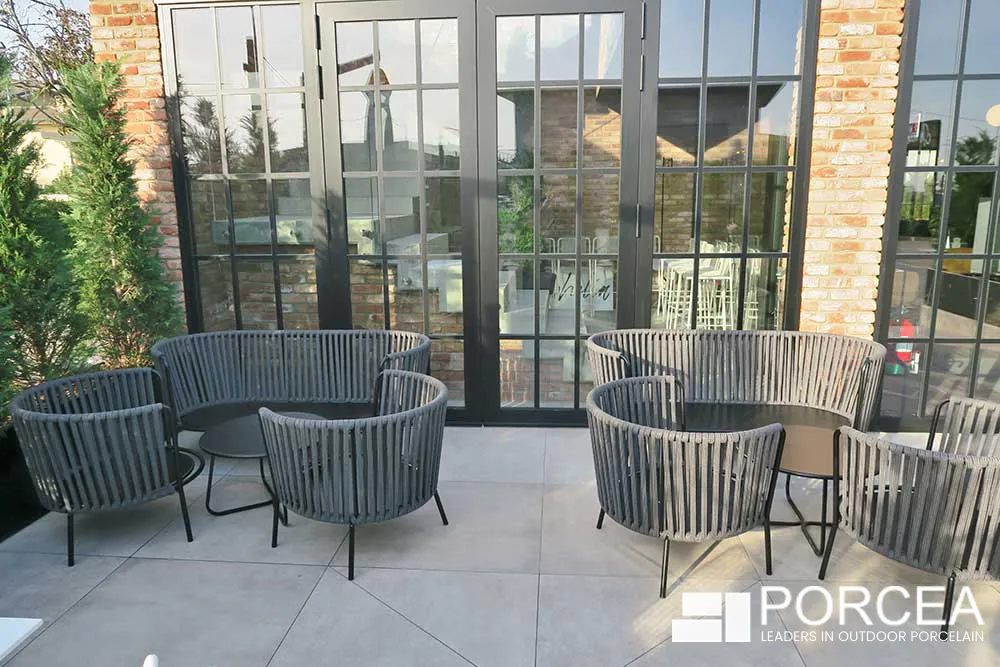
A Quick Look at the Ceramic Industry
The ceramics industry is one of the oldest, dating as far back as 24,000 BC. It all began when humans discovered that mixing clay with water and firing it can produce different kinds of objects.
Today, there's more to ceramics than just clay pots and plates. It's just one of its many aspects. The use of ceramics has evolved into more technical and advanced applications. Also, it encompasses a wide array of materials, including porcelain, cement systems, structural materials, diamonds, graphite, and even glass.
The ceramic industry has two product classifications. These are the traditional or pottery ceramics and advanced ceramics.
Pottery ceramics include the following:
- Porcelain
- Stoneware
- Earthenware
On the other hand, advanced ceramics comprise:
- Bone China
- Fire bricks
- Glass-ceramics
- Tungsten carbide
- Titanium carbide
- Silicon
- Silicon carbide
We are all familiar with clay-based home items, art objects, and construction materials, but pottery is only one aspect of the ceramic world. Nowadays, the term "ceramic" has a broader definition, encompassing materials such as glass, advanced ceramics, and some cement systems.
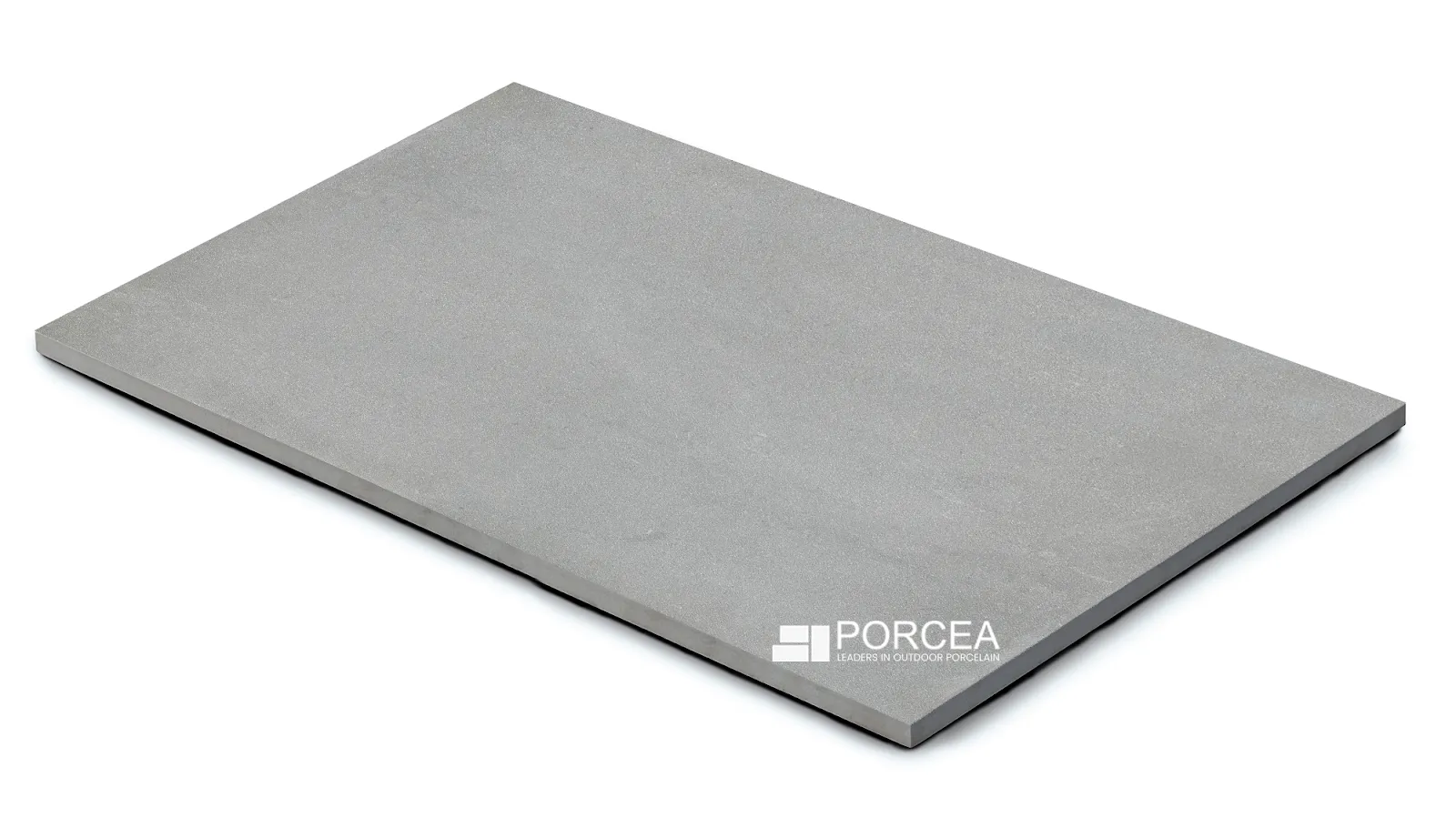
How Porcelain Tiles are Made
Porcelain is one of the most valuable ceramics around. During the 1700s, it made its way to the west, soaring in popularity in North America and Europe. Meanwhile, it is cherished in China because of its unbelievable strength and durability.
As a landscaping material, manufacturers all over the world have been making porcelain tiles for many years. Because this type of ceramics has a low water absorption rate, it is a popular choice of material on walls and floors. The water absorption rate of Porcea Stone products is less than 0.5%. That means it is suitable for all types of weather and allows for high structural strength.
Similar to ceramic, porcelain is made of clay and is kiln-fired. The big difference is in the clay type and temperature used in the production process. Porcelain is made from higher density and very fine clay. Likewise, it is fired at a higher temperature for longer, completely removing all of the moisture from the product. The baking temperature of our outdoor porcelain tiles is 1200°C, resulting in vitrification. Because of this, it is more impervious to water than ceramic tiles. Check out our article about porcelain vs. ceramic tiles to know more about the differences between the two materials.
How are porcelain tiles made? Here is a step-by-step guide to how porcelain tiles are made:
- Raw materials. These will determine the tile's body color and hardness. All raw materials go through batch calculations to ensure they have the right weight to achieve the perfect blend.
- Mix and grind. Next, the raw materials are placed in a mixer, along with water and alumina pebbles. These ball stones aid in grinding the materials into finer particles. This results in a mixture called slip.
- Mixing of colors. Porcelain tiles obtain different colored bodies with the addition of ceramic pigments. Tiles with a natural body coloring skip this process.
- Spray dry. The slip is pumped in an atomizer with nozzles. Then, the rising hot air heats the moisture of the slip and dries it out. As a result, the mixture will turn from liquid to powder form.
- Tile formation. The slip powder form undergoes dry pressing to form the tiles. A steel press compresses the material with more than 7,000 tons of extreme pressure to obtain a less porous and compact ceramic mass.
- Drying. Before firing the tiles, they will undergo a drying process first to get rid of any remaining moisture.
- Adding patterns. Once dried, it's time to add the desired pattern, color, and texture of the tile using a laser inkjet. One benefit of this step is that it helps improve the resistance of the porcelain tiles to staining.
- Glaze. The top of the tile is then applied with a layer of glaze. Aside from decorative purposes, it also helps with the moisture resistance of the product.
- Firing. Afterward, the tiles are kiln-fired at a temperature of 1200°C. This extremely high temperature will remove any remaining moisture and set the glaze. The once soft clay is now a beautiful, non-porous, and durable porcelain tile.
- Rectification. Once the tiles have rested and cooled down, they will show the true colour and pattern that has been applied. The tiles are then rectified (or cut) down to the size that is desired so the edges are all square.
- Quality Control & Packaging. Our automated computer systems will then scan each tile assigning a colour tone and batch number, ensuring grade A material is packaged and labeled with PORCEA STONE branding and colour names.
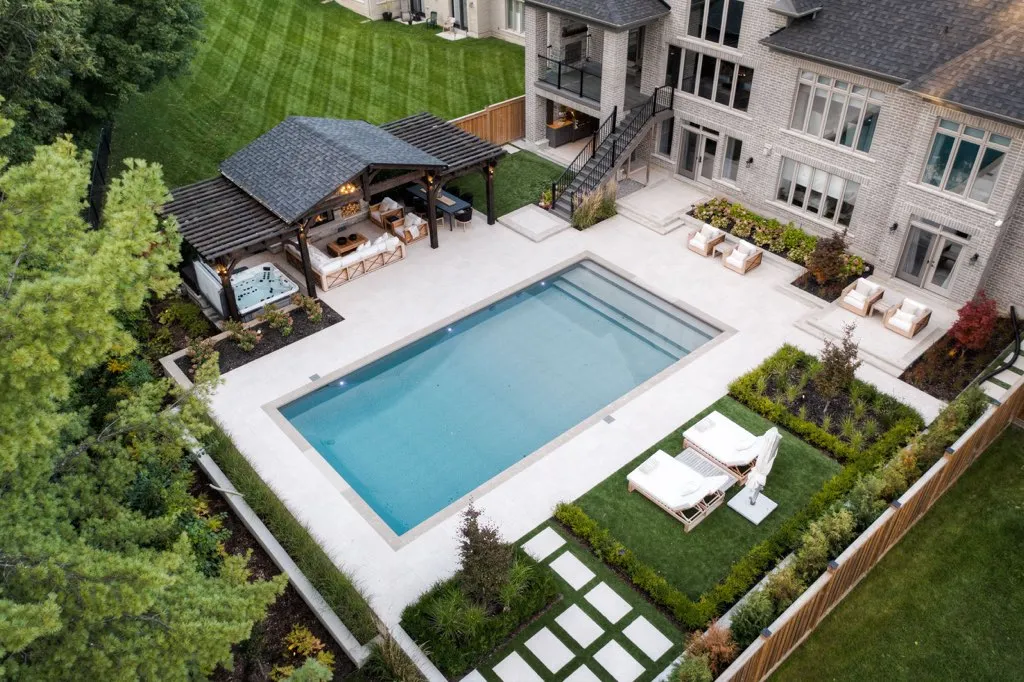
Quality Is In Our DNA
We stand by our products. Our commitment to you from day one is to provide you with only the highest quality outdoor porcelain products that can withstand the harsh North American climate.
We manufacture our beautiful collection of porcelain tiles with adherence to ISO/FDIS 13006:2018 standards. The quality standards for ceramic tiles ensure that our products possess the highest commercial quality. Furthermore, Porcea Stone meets the ASTM (American Society for Testing and Materials) standards, such as:
- Size regularity. This includes length, width, thickness, surface flatness, and rectangularity.
- Water absorption. As mentioned above, our tiles have less than 0.5% absorption of water.
- Breaking load. Our porcelain tiles are highly durable and can resist impact or force.
- Compressive strength. With a MOHS hardness rating ranging between 6-8, the durability of our tiles is comparable to that of granite.
- Frost resistance. Porcea Stone is resistant to freeze-thaw cycles. We test our products at extreme temperatures.
- Skid resistance. All our products have DCOF and slip ratings that exceed R10 and R11.
- Chemical resistance. These highly resilient materials are not prone to chemical staining, as well as acids, mildew, salts, or moss.
- Fire resistance. Since we fire our tiles at a very high temperature of 1,200 °C, they do not exude VOC emissions.
But don't just take our word for it. Experience Porcea Stone for yourself. We take pride in ensuring your satisfaction with the quality of our products. Also, our entire team will work with you every step of the way, from planning to the completion of your landscape project alongside our Authorized Distributors to support your project.
For any questions or concerns, do not hesitate to contact us.
Porcea Stone’s team of experts has more than 20 years of combined experience in the landscaping industry. We specialize in premium outdoor porcelain pavers for residential and commercial applications. As a leader in product innovation, our main focus is on outdoor hardscaping products.
Our wide range of porcelain landscaping stones are designed for application in North America. They are made from the finest materials and engineered to last forever. Aside from this, we take pride in offering our clients exceptional customer service and custom-made solutions to suit their style and budget.
We are consistent with our ground-breaking designs and high technical standards of our products, along with our inherent emphasis on continuous innovation. Because of this, Porcea Stone has become synonymous with excellence in the industry.
A lot has changed over the years we have been in business. Nevertheless, our passion for providing you with premium products and outstanding customer service remains at the very core of what we do.
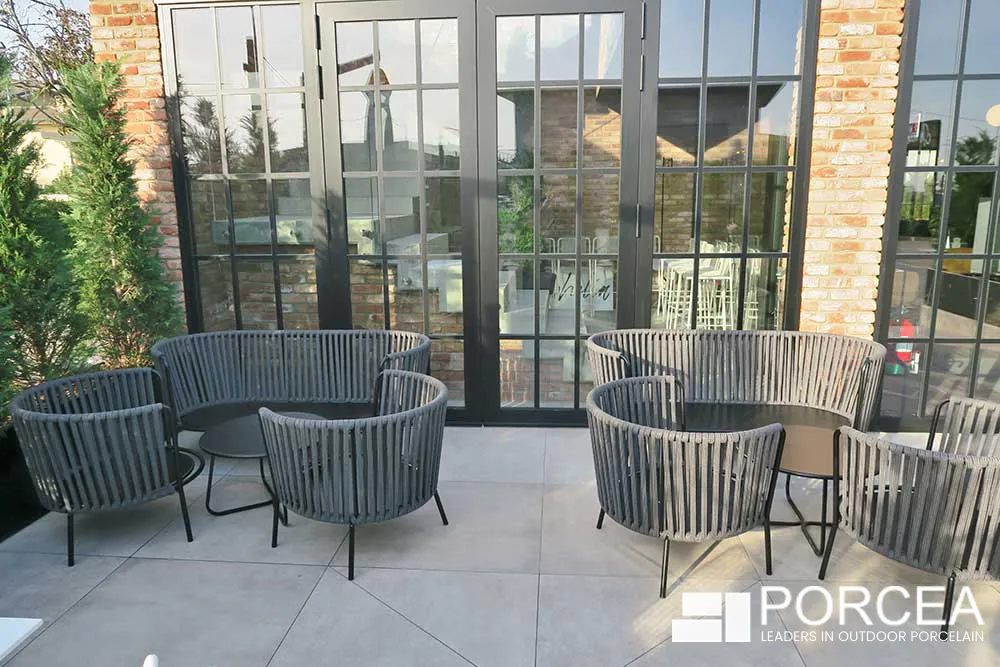
A Quick Look at the Ceramic Industry
The ceramics industry is one of the oldest, dating as far back as 24,000 BC. It all began when humans discovered that mixing clay with water and firing it can produce different kinds of objects.
Today, there's more to ceramics than just clay pots and plates. It's just one of its many aspects. The use of ceramics has evolved into more technical and advanced applications. Also, it encompasses a wide array of materials, including porcelain, cement systems, structural materials, diamonds, graphite, and even glass.
The ceramic industry has two product classifications. These are the traditional or pottery ceramics and advanced ceramics.
Pottery ceramics include the following:
- Porcelain
- Stoneware
- Earthenware
On the other hand, advanced ceramics comprise:
- Bone China
- Fire bricks
- Glass-ceramics
- Tungsten carbide
- Titanium carbide
- Silicon
- Silicon carbide
We are all familiar with clay-based home items, art objects, and construction materials, but pottery is only one aspect of the ceramic world. Nowadays, the term "ceramic" has a broader definition, encompassing materials such as glass, advanced ceramics, and some cement systems.
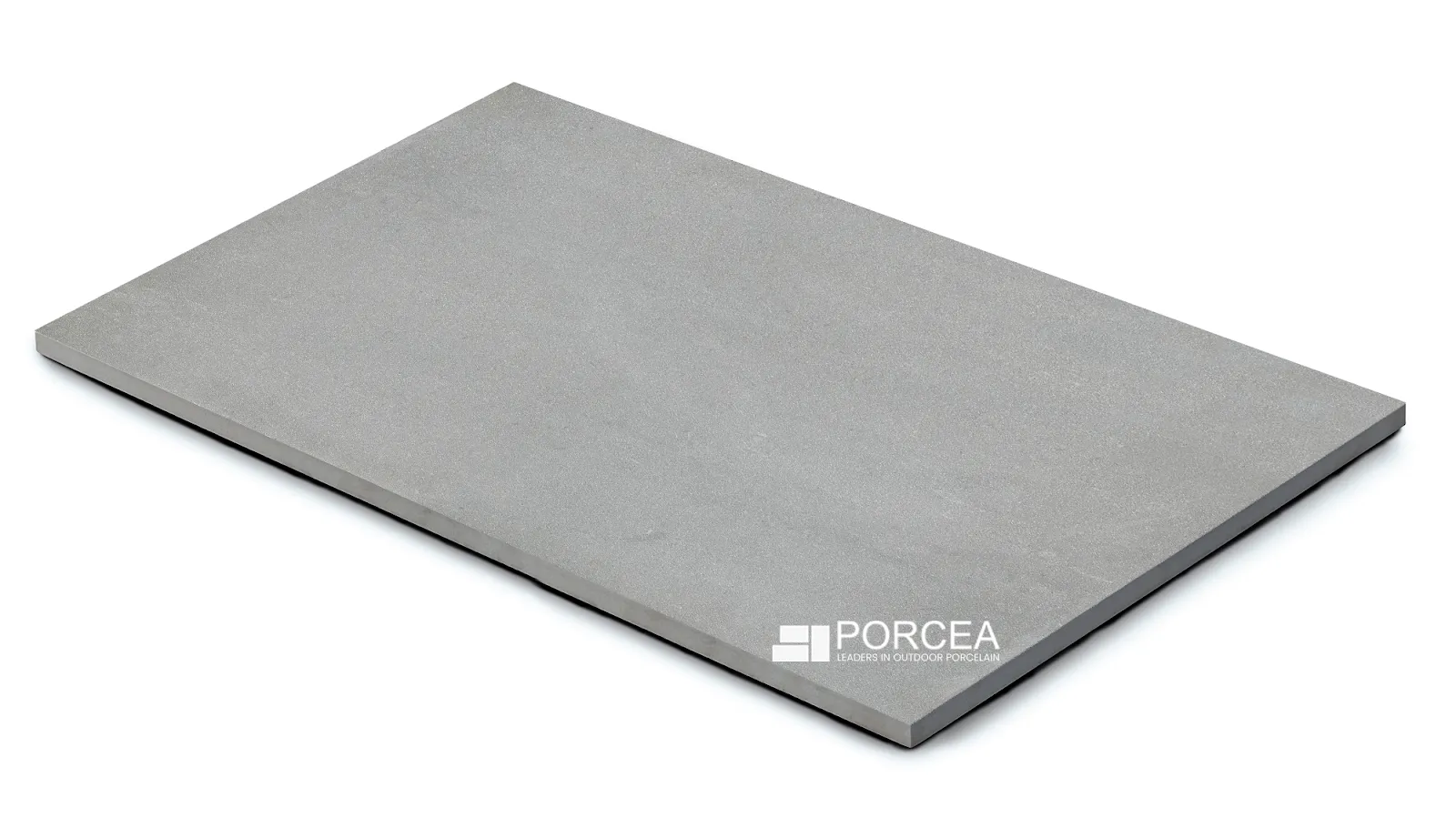
How Porcelain Tiles are Made
Porcelain is one of the most valuable ceramics around. During the 1700s, it made its way to the west, soaring in popularity in North America and Europe. Meanwhile, it is cherished in China because of its unbelievable strength and durability.
As a landscaping material, manufacturers all over the world have been making porcelain tiles for many years. Because this type of ceramics has a low water absorption rate, it is a popular choice of material on walls and floors. The water absorption rate of Porcea Stone products is less than 0.5%. That means it is suitable for all types of weather and allows for high structural strength.
Similar to ceramic, porcelain is made of clay and is kiln-fired. The big difference is in the clay type and temperature used in the production process. Porcelain is made from higher density and very fine clay. Likewise, it is fired at a higher temperature for longer, completely removing all of the moisture from the product. The baking temperature of our outdoor porcelain tiles is 1200°C, resulting in vitrification. Because of this, it is more impervious to water than ceramic tiles. Check out our article about porcelain vs. ceramic tiles to know more about the differences between the two materials.
How are porcelain tiles made? Here is a step-by-step guide to how porcelain tiles are made:
- Raw materials. These will determine the tile's body color and hardness. All raw materials go through batch calculations to ensure they have the right weight to achieve the perfect blend.
- Mix and grind. Next, the raw materials are placed in a mixer, along with water and alumina pebbles. These ball stones aid in grinding the materials into finer particles. This results in a mixture called slip.
- Mixing of colors. Porcelain tiles obtain different colored bodies with the addition of ceramic pigments. Tiles with a natural body coloring skip this process.
- Spray dry. The slip is pumped in an atomizer with nozzles. Then, the rising hot air heats the moisture of the slip and dries it out. As a result, the mixture will turn from liquid to powder form.
- Tile formation. The slip powder form undergoes dry pressing to form the tiles. A steel press compresses the material with more than 7,000 tons of extreme pressure to obtain a less porous and compact ceramic mass.
- Drying. Before firing the tiles, they will undergo a drying process first to get rid of any remaining moisture.
- Adding patterns. Once dried, it's time to add the desired pattern, color, and texture of the tile using a laser inkjet. One benefit of this step is that it helps improve the resistance of the porcelain tiles to staining.
- Glaze. The top of the tile is then applied with a layer of glaze. Aside from decorative purposes, it also helps with the moisture resistance of the product.
- Firing. Afterward, the tiles are kiln-fired at a temperature of 1200°C. This extremely high temperature will remove any remaining moisture and set the glaze. The once soft clay is now a beautiful, non-porous, and durable porcelain tile.
- Rectification. Once the tiles have rested and cooled down, they will show the true colour and pattern that has been applied. The tiles are then rectified (or cut) down to the size that is desired so the edges are all square.
- Quality Control & Packaging. Our automated computer systems will then scan each tile assigning a colour tone and batch number, ensuring grade A material is packaged and labeled with PORCEA STONE branding and colour names.
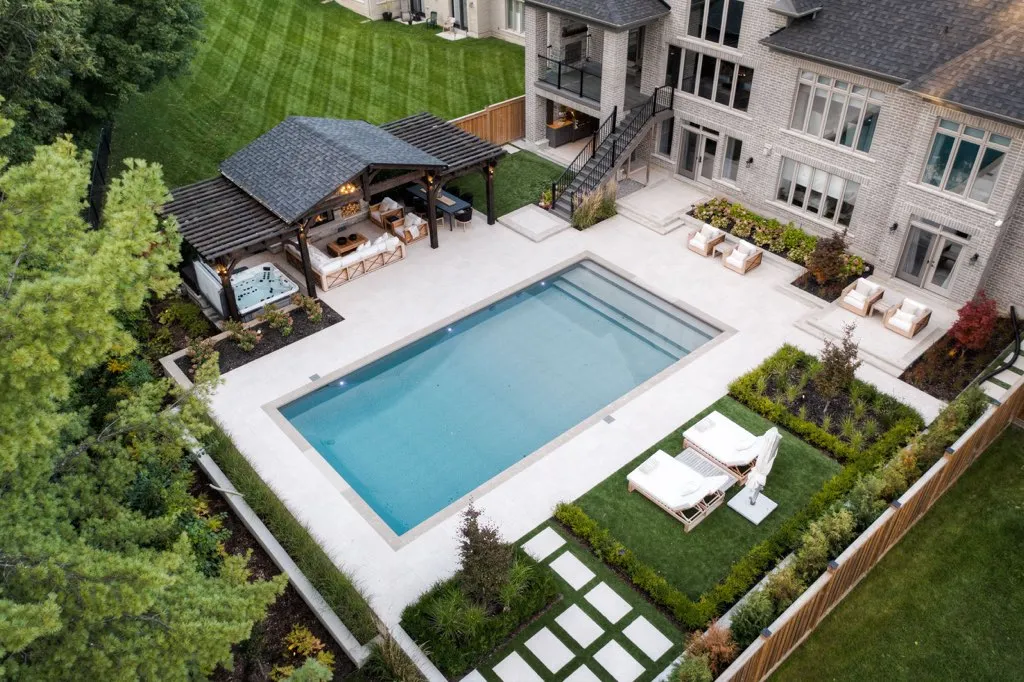
Quality Is In Our DNA
We stand by our products. Our commitment to you from day one is to provide you with only the highest quality outdoor porcelain products that can withstand the harsh North American climate.
We manufacture our beautiful collection of porcelain tiles with adherence to ISO/FDIS 13006:2018 standards. The quality standards for ceramic tiles ensure that our products possess the highest commercial quality. Furthermore, Porcea Stone meets the ASTM (American Society for Testing and Materials) standards, such as:
- Size regularity. This includes length, width, thickness, surface flatness, and rectangularity.
- Water absorption. As mentioned above, our tiles have less than 0.5% absorption of water.
- Breaking load. Our porcelain tiles are highly durable and can resist impact or force.
- Compressive strength. With a MOHS hardness rating ranging between 6-8, the durability of our tiles is comparable to that of granite.
- Frost resistance. Porcea Stone is resistant to freeze-thaw cycles. We test our products at extreme temperatures.
- Skid resistance. All our products have DCOF and slip ratings that exceed R10 and R11.
- Chemical resistance. These highly resilient materials are not prone to chemical staining, as well as acids, mildew, salts, or moss.
- Fire resistance. Since we fire our tiles at a very high temperature of 1,200 °C, they do not exude VOC emissions.
But don't just take our word for it. Experience Porcea Stone for yourself. We take pride in ensuring your satisfaction with the quality of our products. Also, our entire team will work with you every step of the way, from planning to the completion of your landscape project alongside our Authorized Distributors to support your project.
For any questions or concerns, do not hesitate to contact us.
Porcea Stone’s team of experts has more than 20 years of combined experience in the landscaping industry. We specialize in premium outdoor porcelain pavers for residential and commercial applications. As a leader in product innovation, our main focus is on outdoor hardscaping products.
Our wide range of porcelain landscaping stones are designed for application in North America. They are made from the finest materials and engineered to last forever. Aside from this, we take pride in offering our clients exceptional customer service and custom-made solutions to suit their style and budget.
We are consistent with our ground-breaking designs and high technical standards of our products, along with our inherent emphasis on continuous innovation. Because of this, Porcea Stone has become synonymous with excellence in the industry.
A lot has changed over the years we have been in business. Nevertheless, our passion for providing you with premium products and outstanding customer service remains at the very core of what we do.
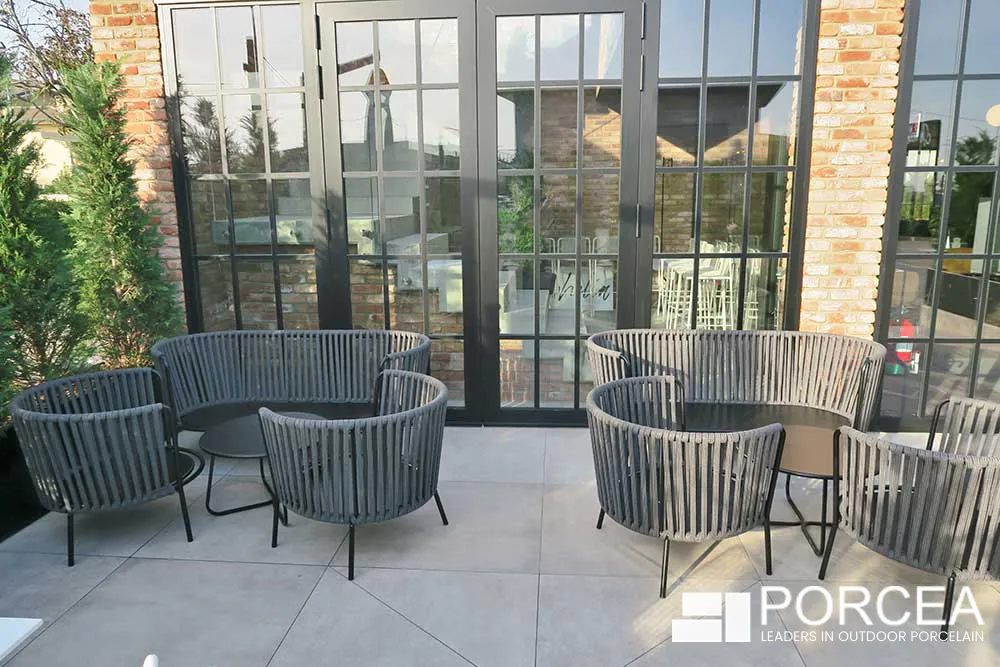
A Quick Look at the Ceramic Industry
The ceramics industry is one of the oldest, dating as far back as 24,000 BC. It all began when humans discovered that mixing clay with water and firing it can produce different kinds of objects.
Today, there's more to ceramics than just clay pots and plates. It's just one of its many aspects. The use of ceramics has evolved into more technical and advanced applications. Also, it encompasses a wide array of materials, including porcelain, cement systems, structural materials, diamonds, graphite, and even glass.
The ceramic industry has two product classifications. These are the traditional or pottery ceramics and advanced ceramics.
Pottery ceramics include the following:
- Porcelain
- Stoneware
- Earthenware
On the other hand, advanced ceramics comprise:
- Bone China
- Fire bricks
- Glass-ceramics
- Tungsten carbide
- Titanium carbide
- Silicon
- Silicon carbide
We are all familiar with clay-based home items, art objects, and construction materials, but pottery is only one aspect of the ceramic world. Nowadays, the term "ceramic" has a broader definition, encompassing materials such as glass, advanced ceramics, and some cement systems.
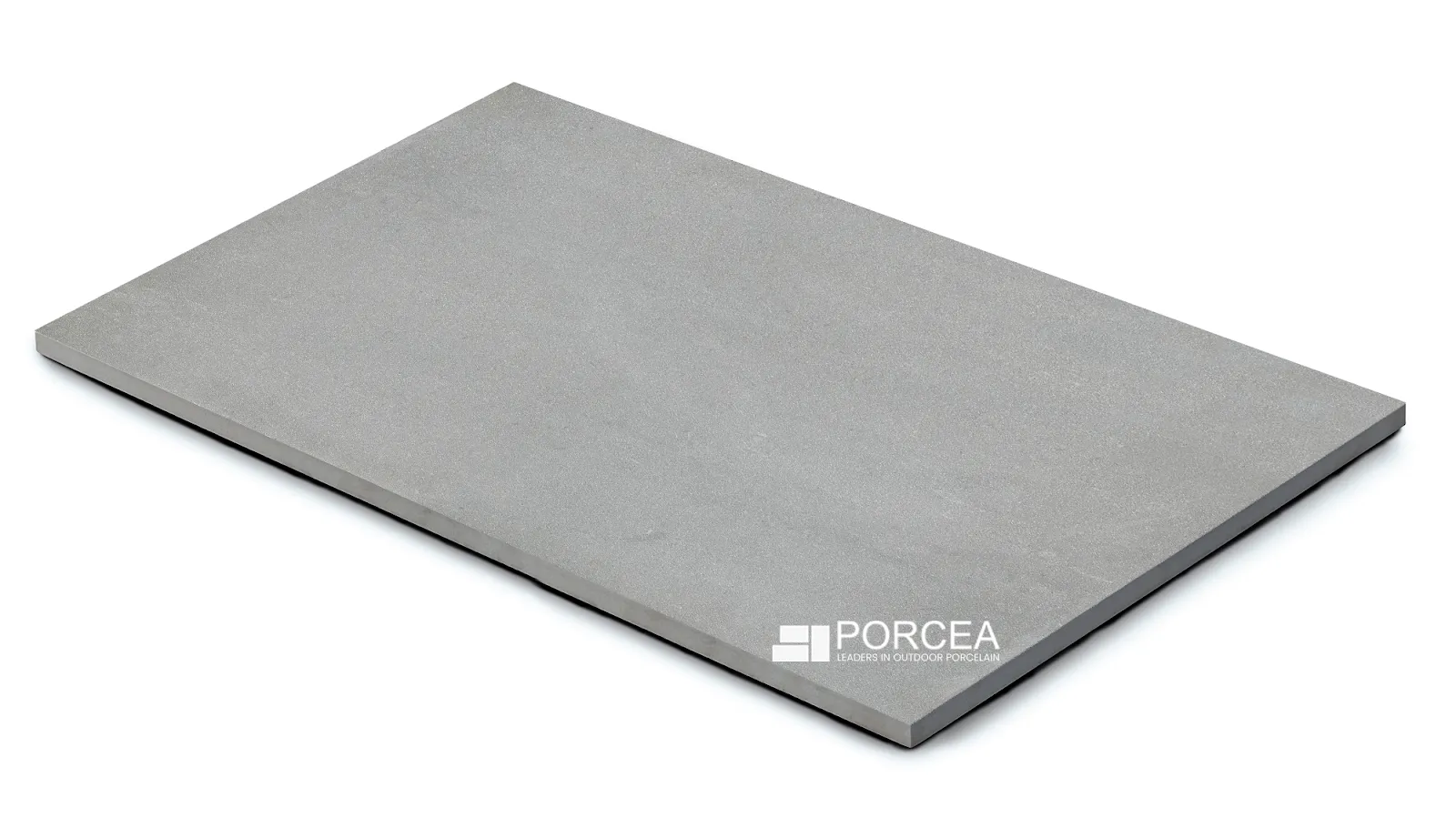
How Porcelain Tiles are Made
Porcelain is one of the most valuable ceramics around. During the 1700s, it made its way to the west, soaring in popularity in North America and Europe. Meanwhile, it is cherished in China because of its unbelievable strength and durability.
As a landscaping material, manufacturers all over the world have been making porcelain tiles for many years. Because this type of ceramics has a low water absorption rate, it is a popular choice of material on walls and floors. The water absorption rate of Porcea Stone products is less than 0.5%. That means it is suitable for all types of weather and allows for high structural strength.
Similar to ceramic, porcelain is made of clay and is kiln-fired. The big difference is in the clay type and temperature used in the production process. Porcelain is made from higher density and very fine clay. Likewise, it is fired at a higher temperature for longer, completely removing all of the moisture from the product. The baking temperature of our outdoor porcelain tiles is 1200°C, resulting in vitrification. Because of this, it is more impervious to water than ceramic tiles. Check out our article about porcelain vs. ceramic tiles to know more about the differences between the two materials.
How are porcelain tiles made? Here is a step-by-step guide to how porcelain tiles are made:
- Raw materials. These will determine the tile's body color and hardness. All raw materials go through batch calculations to ensure they have the right weight to achieve the perfect blend.
- Mix and grind. Next, the raw materials are placed in a mixer, along with water and alumina pebbles. These ball stones aid in grinding the materials into finer particles. This results in a mixture called slip.
- Mixing of colors. Porcelain tiles obtain different colored bodies with the addition of ceramic pigments. Tiles with a natural body coloring skip this process.
- Spray dry. The slip is pumped in an atomizer with nozzles. Then, the rising hot air heats the moisture of the slip and dries it out. As a result, the mixture will turn from liquid to powder form.
- Tile formation. The slip powder form undergoes dry pressing to form the tiles. A steel press compresses the material with more than 7,000 tons of extreme pressure to obtain a less porous and compact ceramic mass.
- Drying. Before firing the tiles, they will undergo a drying process first to get rid of any remaining moisture.
- Adding patterns. Once dried, it's time to add the desired pattern, color, and texture of the tile using a laser inkjet. One benefit of this step is that it helps improve the resistance of the porcelain tiles to staining.
- Glaze. The top of the tile is then applied with a layer of glaze. Aside from decorative purposes, it also helps with the moisture resistance of the product.
- Firing. Afterward, the tiles are kiln-fired at a temperature of 1200°C. This extremely high temperature will remove any remaining moisture and set the glaze. The once soft clay is now a beautiful, non-porous, and durable porcelain tile.
- Rectification. Once the tiles have rested and cooled down, they will show the true colour and pattern that has been applied. The tiles are then rectified (or cut) down to the size that is desired so the edges are all square.
- Quality Control & Packaging. Our automated computer systems will then scan each tile assigning a colour tone and batch number, ensuring grade A material is packaged and labeled with PORCEA STONE branding and colour names.
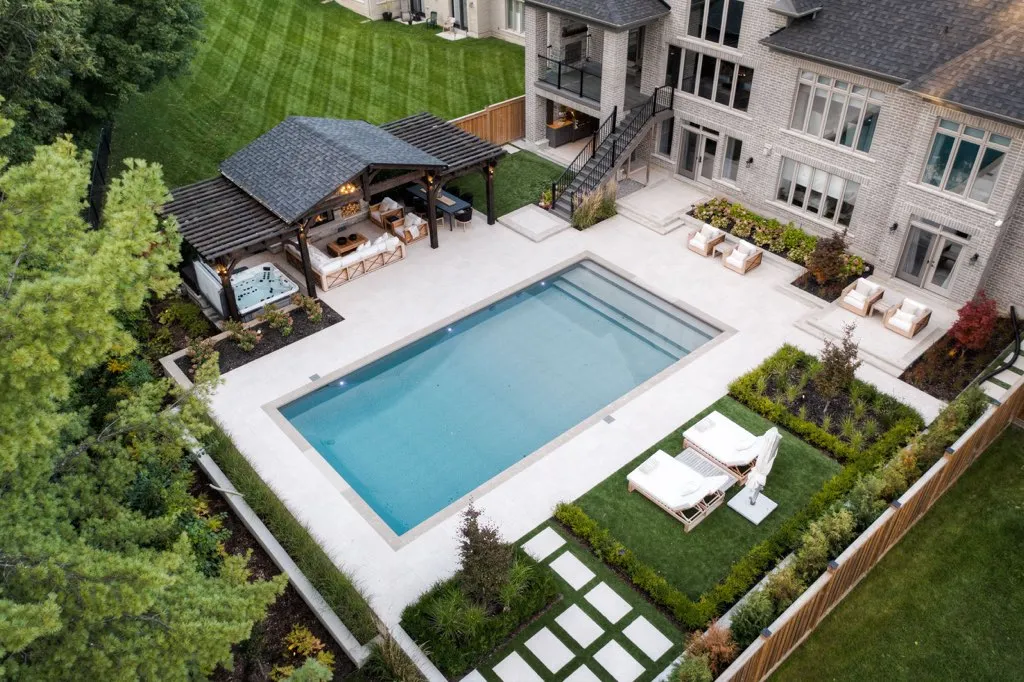
Quality Is In Our DNA
We stand by our products. Our commitment to you from day one is to provide you with only the highest quality outdoor porcelain products that can withstand the harsh North American climate.
We manufacture our beautiful collection of porcelain tiles with adherence to ISO/FDIS 13006:2018 standards. The quality standards for ceramic tiles ensure that our products possess the highest commercial quality. Furthermore, Porcea Stone meets the ASTM (American Society for Testing and Materials) standards, such as:
- Size regularity. This includes length, width, thickness, surface flatness, and rectangularity.
- Water absorption. As mentioned above, our tiles have less than 0.5% absorption of water.
- Breaking load. Our porcelain tiles are highly durable and can resist impact or force.
- Compressive strength. With a MOHS hardness rating ranging between 6-8, the durability of our tiles is comparable to that of granite.
- Frost resistance. Porcea Stone is resistant to freeze-thaw cycles. We test our products at extreme temperatures.
- Skid resistance. All our products have DCOF and slip ratings that exceed R10 and R11.
- Chemical resistance. These highly resilient materials are not prone to chemical staining, as well as acids, mildew, salts, or moss.
- Fire resistance. Since we fire our tiles at a very high temperature of 1,200 °C, they do not exude VOC emissions.
But don't just take our word for it. Experience Porcea Stone for yourself. We take pride in ensuring your satisfaction with the quality of our products. Also, our entire team will work with you every step of the way, from planning to the completion of your landscape project alongside our Authorized Distributors to support your project.
For any questions or concerns, do not hesitate to contact us.
Porcea Stone’s team of experts has more than 20 years of combined experience in the landscaping industry. We specialize in premium outdoor porcelain pavers for residential and commercial applications. As a leader in product innovation, our main focus is on outdoor hardscaping products.
Our wide range of porcelain landscaping stones are designed for application in North America. They are made from the finest materials and engineered to last forever. Aside from this, we take pride in offering our clients exceptional customer service and custom-made solutions to suit their style and budget.
We are consistent with our ground-breaking designs and high technical standards of our products, along with our inherent emphasis on continuous innovation. Because of this, Porcea Stone has become synonymous with excellence in the industry.
A lot has changed over the years we have been in business. Nevertheless, our passion for providing you with premium products and outstanding customer service remains at the very core of what we do.
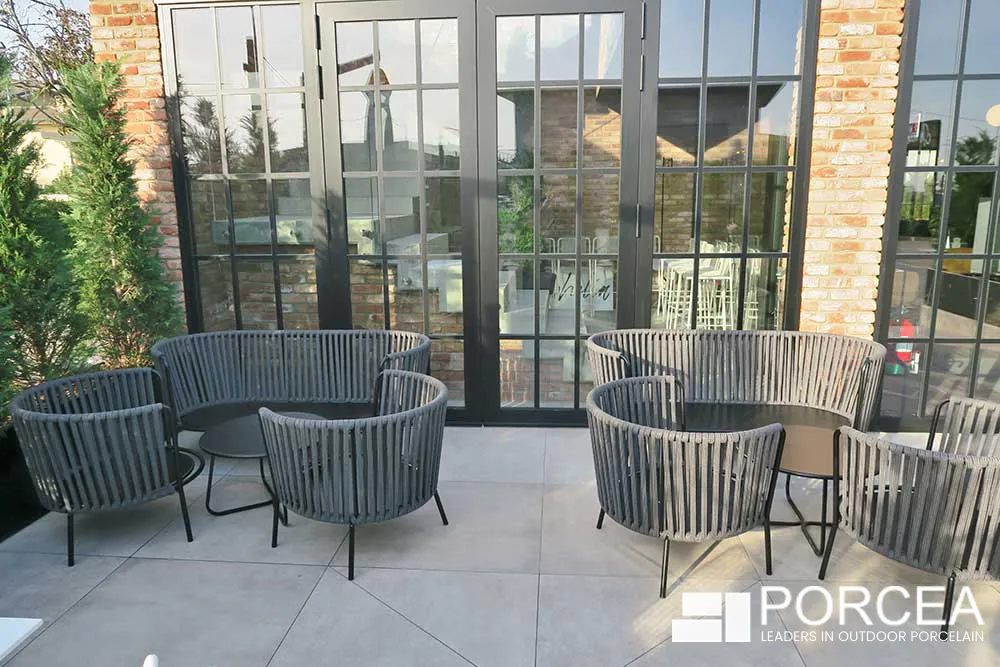
A Quick Look at the Ceramic Industry
The ceramics industry is one of the oldest, dating as far back as 24,000 BC. It all began when humans discovered that mixing clay with water and firing it can produce different kinds of objects.
Today, there's more to ceramics than just clay pots and plates. It's just one of its many aspects. The use of ceramics has evolved into more technical and advanced applications. Also, it encompasses a wide array of materials, including porcelain, cement systems, structural materials, diamonds, graphite, and even glass.
The ceramic industry has two product classifications. These are the traditional or pottery ceramics and advanced ceramics.
Pottery ceramics include the following:
- Porcelain
- Stoneware
- Earthenware
On the other hand, advanced ceramics comprise:
- Bone China
- Fire bricks
- Glass-ceramics
- Tungsten carbide
- Titanium carbide
- Silicon
- Silicon carbide
We are all familiar with clay-based home items, art objects, and construction materials, but pottery is only one aspect of the ceramic world. Nowadays, the term "ceramic" has a broader definition, encompassing materials such as glass, advanced ceramics, and some cement systems.
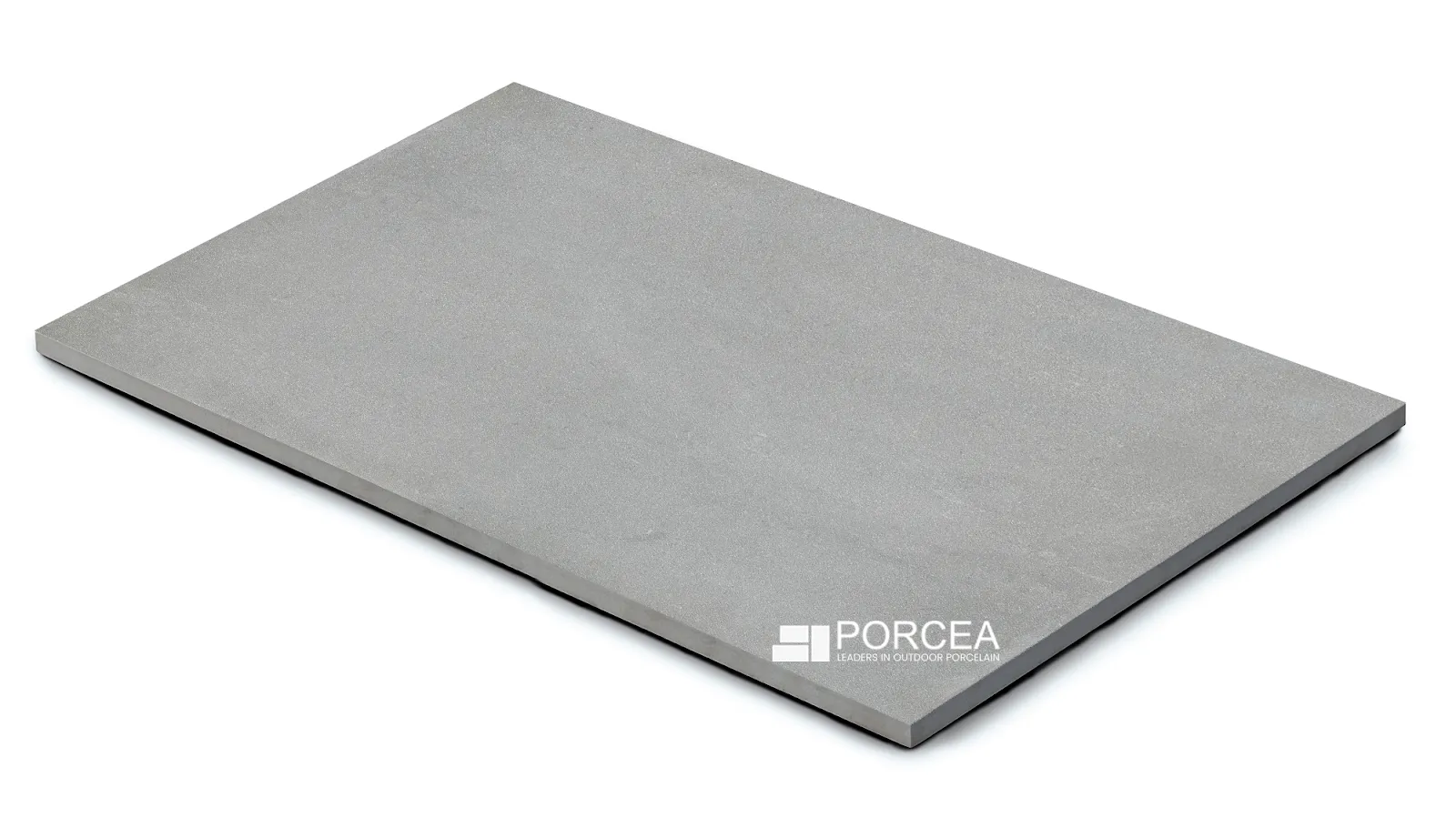
How Porcelain Tiles are Made
Porcelain is one of the most valuable ceramics around. During the 1700s, it made its way to the west, soaring in popularity in North America and Europe. Meanwhile, it is cherished in China because of its unbelievable strength and durability.
As a landscaping material, manufacturers all over the world have been making porcelain tiles for many years. Because this type of ceramics has a low water absorption rate, it is a popular choice of material on walls and floors. The water absorption rate of Porcea Stone products is less than 0.5%. That means it is suitable for all types of weather and allows for high structural strength.
Similar to ceramic, porcelain is made of clay and is kiln-fired. The big difference is in the clay type and temperature used in the production process. Porcelain is made from higher density and very fine clay. Likewise, it is fired at a higher temperature for longer, completely removing all of the moisture from the product. The baking temperature of our outdoor porcelain tiles is 1200°C, resulting in vitrification. Because of this, it is more impervious to water than ceramic tiles. Check out our article about porcelain vs. ceramic tiles to know more about the differences between the two materials.
How are porcelain tiles made? Here is a step-by-step guide to how porcelain tiles are made:
- Raw materials. These will determine the tile's body color and hardness. All raw materials go through batch calculations to ensure they have the right weight to achieve the perfect blend.
- Mix and grind. Next, the raw materials are placed in a mixer, along with water and alumina pebbles. These ball stones aid in grinding the materials into finer particles. This results in a mixture called slip.
- Mixing of colors. Porcelain tiles obtain different colored bodies with the addition of ceramic pigments. Tiles with a natural body coloring skip this process.
- Spray dry. The slip is pumped in an atomizer with nozzles. Then, the rising hot air heats the moisture of the slip and dries it out. As a result, the mixture will turn from liquid to powder form.
- Tile formation. The slip powder form undergoes dry pressing to form the tiles. A steel press compresses the material with more than 7,000 tons of extreme pressure to obtain a less porous and compact ceramic mass.
- Drying. Before firing the tiles, they will undergo a drying process first to get rid of any remaining moisture.
- Adding patterns. Once dried, it's time to add the desired pattern, color, and texture of the tile using a laser inkjet. One benefit of this step is that it helps improve the resistance of the porcelain tiles to staining.
- Glaze. The top of the tile is then applied with a layer of glaze. Aside from decorative purposes, it also helps with the moisture resistance of the product.
- Firing. Afterward, the tiles are kiln-fired at a temperature of 1200°C. This extremely high temperature will remove any remaining moisture and set the glaze. The once soft clay is now a beautiful, non-porous, and durable porcelain tile.
- Rectification. Once the tiles have rested and cooled down, they will show the true colour and pattern that has been applied. The tiles are then rectified (or cut) down to the size that is desired so the edges are all square.
- Quality Control & Packaging. Our automated computer systems will then scan each tile assigning a colour tone and batch number, ensuring grade A material is packaged and labeled with PORCEA STONE branding and colour names.
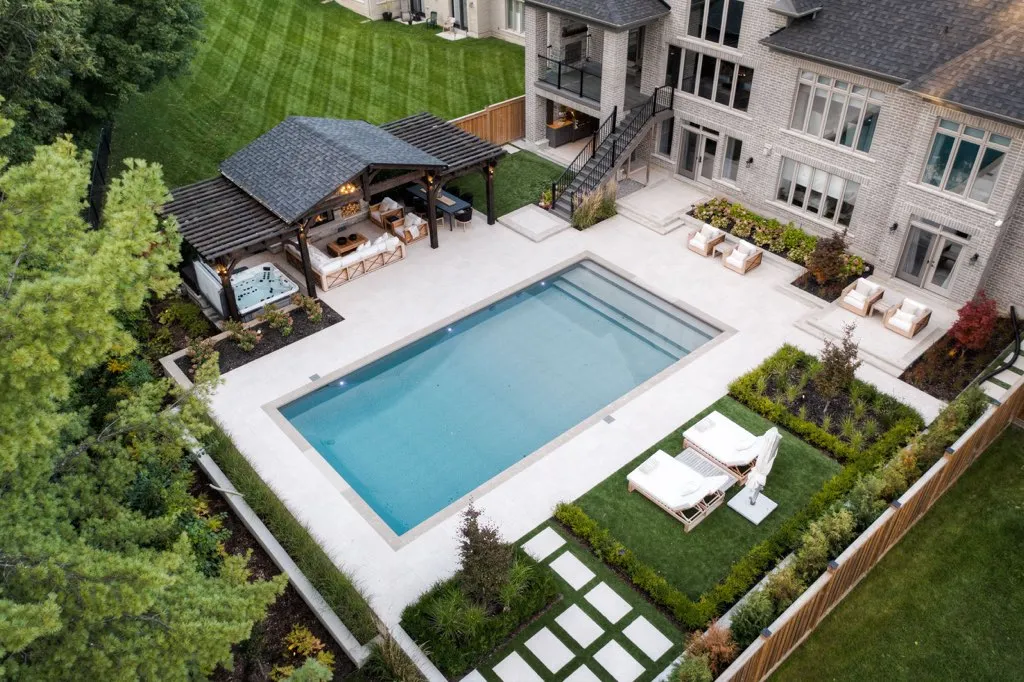
Quality Is In Our DNA
We stand by our products. Our commitment to you from day one is to provide you with only the highest quality outdoor porcelain products that can withstand the harsh North American climate.
We manufacture our beautiful collection of porcelain tiles with adherence to ISO/FDIS 13006:2018 standards. The quality standards for ceramic tiles ensure that our products possess the highest commercial quality. Furthermore, Porcea Stone meets the ASTM (American Society for Testing and Materials) standards, such as:
- Size regularity. This includes length, width, thickness, surface flatness, and rectangularity.
- Water absorption. As mentioned above, our tiles have less than 0.5% absorption of water.
- Breaking load. Our porcelain tiles are highly durable and can resist impact or force.
- Compressive strength. With a MOHS hardness rating ranging between 6-8, the durability of our tiles is comparable to that of granite.
- Frost resistance. Porcea Stone is resistant to freeze-thaw cycles. We test our products at extreme temperatures.
- Skid resistance. All our products have DCOF and slip ratings that exceed R10 and R11.
- Chemical resistance. These highly resilient materials are not prone to chemical staining, as well as acids, mildew, salts, or moss.
- Fire resistance. Since we fire our tiles at a very high temperature of 1,200 °C, they do not exude VOC emissions.
But don't just take our word for it. Experience Porcea Stone for yourself. We take pride in ensuring your satisfaction with the quality of our products. Also, our entire team will work with you every step of the way, from planning to the completion of your landscape project alongside our Authorized Distributors to support your project.
For any questions or concerns, do not hesitate to contact us.
Porcea Stone’s team of experts has more than 20 years of combined experience in the landscaping industry. We specialize in premium outdoor porcelain pavers for residential and commercial applications. As a leader in product innovation, our main focus is on outdoor hardscaping products.
Our wide range of porcelain landscaping stones are designed for application in North America. They are made from the finest materials and engineered to last forever. Aside from this, we take pride in offering our clients exceptional customer service and custom-made solutions to suit their style and budget.
We are consistent with our ground-breaking designs and high technical standards of our products, along with our inherent emphasis on continuous innovation. Because of this, Porcea Stone has become synonymous with excellence in the industry.
A lot has changed over the years we have been in business. Nevertheless, our passion for providing you with premium products and outstanding customer service remains at the very core of what we do.
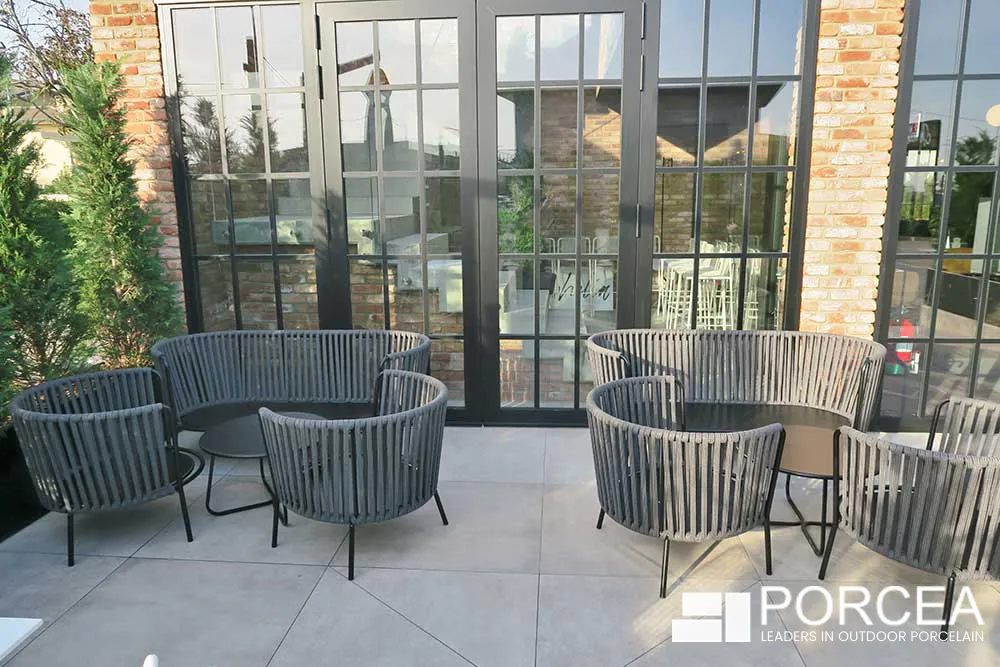
A Quick Look at the Ceramic Industry
The ceramics industry is one of the oldest, dating as far back as 24,000 BC. It all began when humans discovered that mixing clay with water and firing it can produce different kinds of objects.
Today, there's more to ceramics than just clay pots and plates. It's just one of its many aspects. The use of ceramics has evolved into more technical and advanced applications. Also, it encompasses a wide array of materials, including porcelain, cement systems, structural materials, diamonds, graphite, and even glass.
The ceramic industry has two product classifications. These are the traditional or pottery ceramics and advanced ceramics.
Pottery ceramics include the following:
- Porcelain
- Stoneware
- Earthenware
On the other hand, advanced ceramics comprise:
- Bone China
- Fire bricks
- Glass-ceramics
- Tungsten carbide
- Titanium carbide
- Silicon
- Silicon carbide
We are all familiar with clay-based home items, art objects, and construction materials, but pottery is only one aspect of the ceramic world. Nowadays, the term "ceramic" has a broader definition, encompassing materials such as glass, advanced ceramics, and some cement systems.
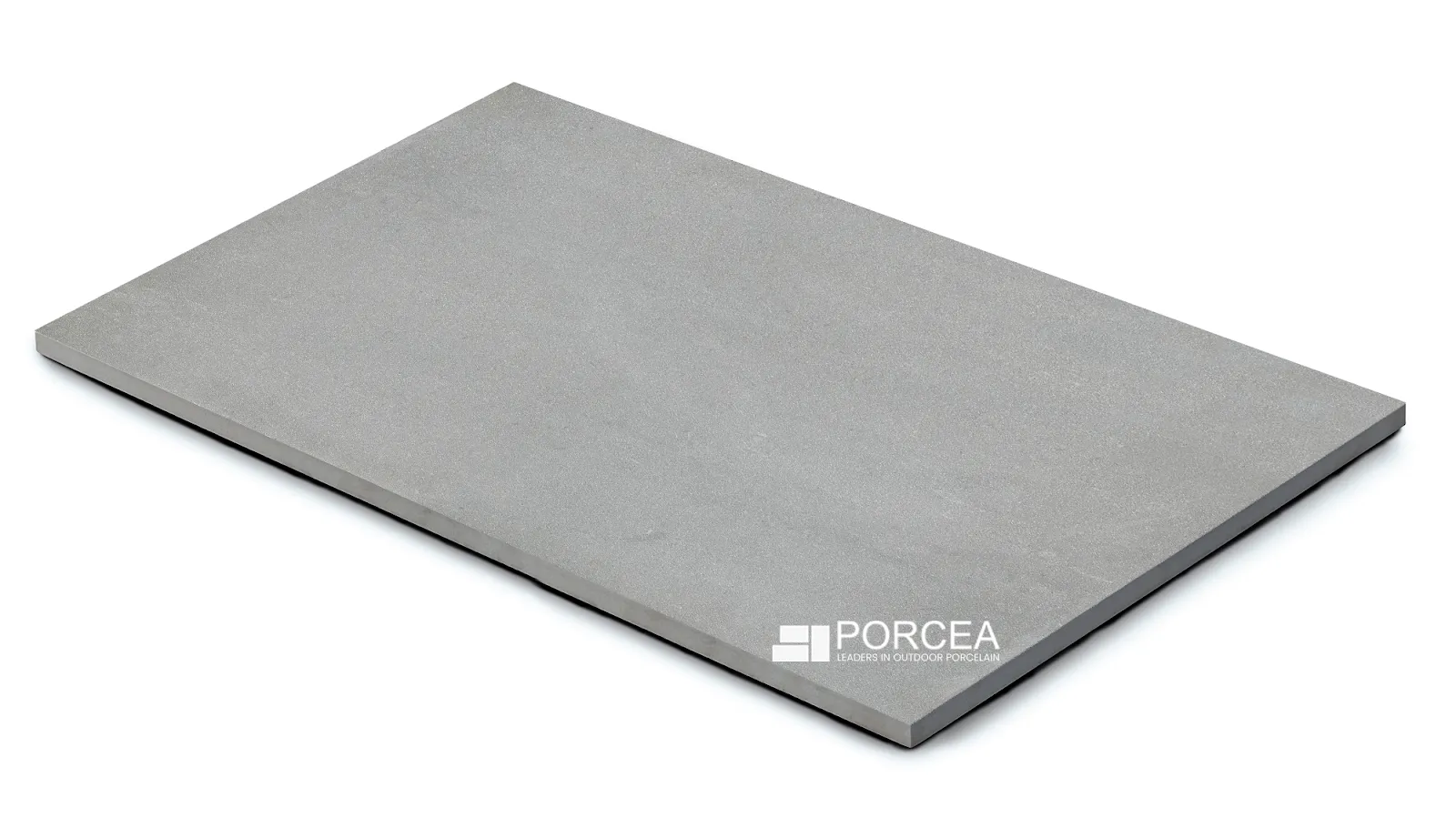
How Porcelain Tiles are Made
Porcelain is one of the most valuable ceramics around. During the 1700s, it made its way to the west, soaring in popularity in North America and Europe. Meanwhile, it is cherished in China because of its unbelievable strength and durability.
As a landscaping material, manufacturers all over the world have been making porcelain tiles for many years. Because this type of ceramics has a low water absorption rate, it is a popular choice of material on walls and floors. The water absorption rate of Porcea Stone products is less than 0.5%. That means it is suitable for all types of weather and allows for high structural strength.
Similar to ceramic, porcelain is made of clay and is kiln-fired. The big difference is in the clay type and temperature used in the production process. Porcelain is made from higher density and very fine clay. Likewise, it is fired at a higher temperature for longer, completely removing all of the moisture from the product. The baking temperature of our outdoor porcelain tiles is 1200°C, resulting in vitrification. Because of this, it is more impervious to water than ceramic tiles. Check out our article about porcelain vs. ceramic tiles to know more about the differences between the two materials.
How are porcelain tiles made? Here is a step-by-step guide to how porcelain tiles are made:
- Raw materials. These will determine the tile's body color and hardness. All raw materials go through batch calculations to ensure they have the right weight to achieve the perfect blend.
- Mix and grind. Next, the raw materials are placed in a mixer, along with water and alumina pebbles. These ball stones aid in grinding the materials into finer particles. This results in a mixture called slip.
- Mixing of colors. Porcelain tiles obtain different colored bodies with the addition of ceramic pigments. Tiles with a natural body coloring skip this process.
- Spray dry. The slip is pumped in an atomizer with nozzles. Then, the rising hot air heats the moisture of the slip and dries it out. As a result, the mixture will turn from liquid to powder form.
- Tile formation. The slip powder form undergoes dry pressing to form the tiles. A steel press compresses the material with more than 7,000 tons of extreme pressure to obtain a less porous and compact ceramic mass.
- Drying. Before firing the tiles, they will undergo a drying process first to get rid of any remaining moisture.
- Adding patterns. Once dried, it's time to add the desired pattern, color, and texture of the tile using a laser inkjet. One benefit of this step is that it helps improve the resistance of the porcelain tiles to staining.
- Glaze. The top of the tile is then applied with a layer of glaze. Aside from decorative purposes, it also helps with the moisture resistance of the product.
- Firing. Afterward, the tiles are kiln-fired at a temperature of 1200°C. This extremely high temperature will remove any remaining moisture and set the glaze. The once soft clay is now a beautiful, non-porous, and durable porcelain tile.
- Rectification. Once the tiles have rested and cooled down, they will show the true colour and pattern that has been applied. The tiles are then rectified (or cut) down to the size that is desired so the edges are all square.
- Quality Control & Packaging. Our automated computer systems will then scan each tile assigning a colour tone and batch number, ensuring grade A material is packaged and labeled with PORCEA STONE branding and colour names.
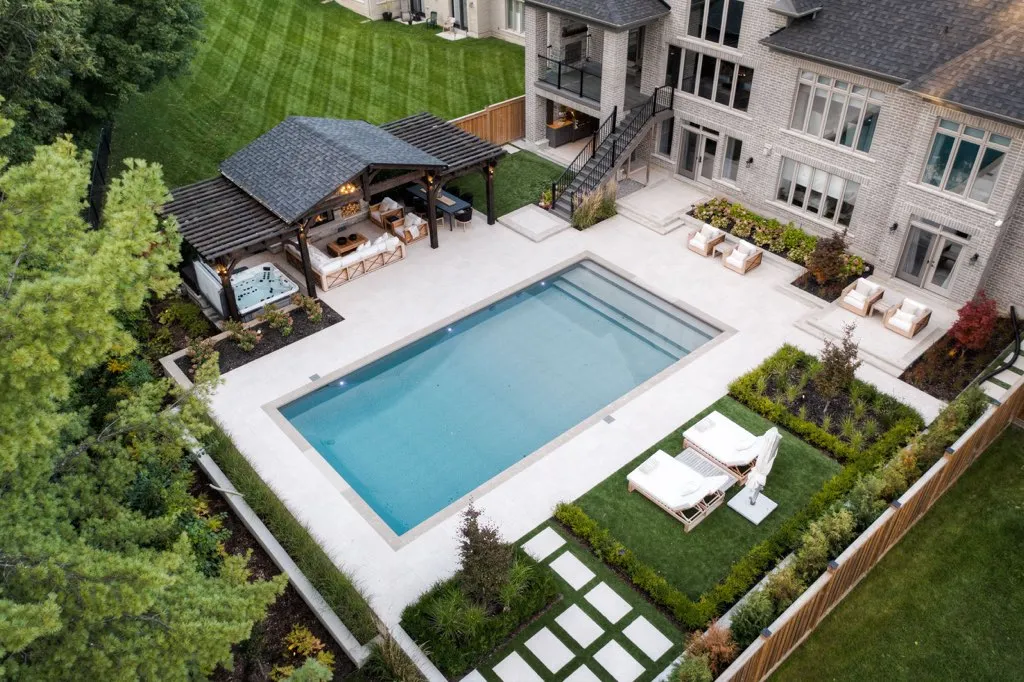
Quality Is In Our DNA
We stand by our products. Our commitment to you from day one is to provide you with only the highest quality outdoor porcelain products that can withstand the harsh North American climate.
We manufacture our beautiful collection of porcelain tiles with adherence to ISO/FDIS 13006:2018 standards. The quality standards for ceramic tiles ensure that our products possess the highest commercial quality. Furthermore, Porcea Stone meets the ASTM (American Society for Testing and Materials) standards, such as:
- Size regularity. This includes length, width, thickness, surface flatness, and rectangularity.
- Water absorption. As mentioned above, our tiles have less than 0.5% absorption of water.
- Breaking load. Our porcelain tiles are highly durable and can resist impact or force.
- Compressive strength. With a MOHS hardness rating ranging between 6-8, the durability of our tiles is comparable to that of granite.
- Frost resistance. Porcea Stone is resistant to freeze-thaw cycles. We test our products at extreme temperatures.
- Skid resistance. All our products have DCOF and slip ratings that exceed R10 and R11.
- Chemical resistance. These highly resilient materials are not prone to chemical staining, as well as acids, mildew, salts, or moss.
- Fire resistance. Since we fire our tiles at a very high temperature of 1,200 °C, they do not exude VOC emissions.
But don't just take our word for it. Experience Porcea Stone for yourself. We take pride in ensuring your satisfaction with the quality of our products. Also, our entire team will work with you every step of the way, from planning to the completion of your landscape project alongside our Authorized Distributors to support your project.
For any questions or concerns, do not hesitate to contact us.